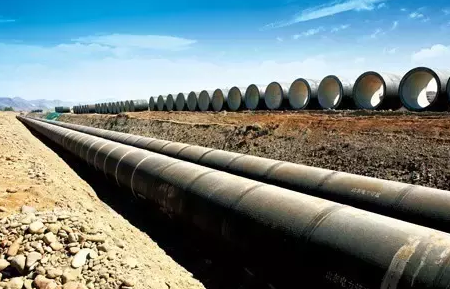
管道防腐层是在埋地管道表面用于防腐蚀的保护层,也是管道长期安全运行的关键,在实际使用过程中防腐层会出现起泡现象,也是一个常见的问题,防腐层起泡可能由多种原因引起。
一、 泡的特征及分类
起泡区域的共同特性是泡首先产生在胶带附着力最弱点的地方。泡有大有小,以单个或群体的方式存在。泡内可能含液体、蒸汽、其他气体货结晶物、但也可以是干泡,按泡内所含物质可分为气泡、水泡和加渣泡。起泡通常是伴随涂料固化或胶层老化过程发生的,从此意义上说,起泡可分为膨胀起泡和腐蚀起泡两种。在任何时候,起泡的结果可能是泡的尺寸变大,集合在一起,形成大面积脱层,产生表面缺陷,导致防腐效果下降,甚至消失。
二、 起泡的原因分析
泡的形成尽管最初可能有多种,但最主要最常见的原因是由于涂层内存在潮湿蒸汽或其它蒸汽等,例如:空气或溶剂蒸汽。由于胶层在早晨的阳光中受热,然后处于夜间低温和潮湿的条件下,当防腐层内的蒸汽因温度升高而膨胀,通常首先出现起泡。起泡的大小,取决于胶带对底漆钢的附着力、泡内液体或气体的压力。此类起泡的原因可能有以下几个方面:
1、底漆中的可溶性配方:某些原料在潮湿蒸汽透过涂膜时,能将其吸收或者甚至可能将潮气吸入涂膜以满足其吸湿性,完成防腐体系时,底漆固化后,可能会由于温度升高等原因,潮湿蒸汽从颜料中挥发出,形成气泡。
2、可溶性化学盐类:施工过程中,钢管或底漆涂层处理不当,可溶性化学盐类呗保留在底材货涂层之间,则会发生渗透作用,将更多的潮气吸入涂层,导致涂层起泡。
3、其它污染物:底材上或涂层表面如果存在油、蜡或灰尘等污染物,则会导致防腐胶带的附着力不好。潮湿蒸汽会透过涂层进入此类区域,从而保留在哪里,当由于温度变化等原因造成蒸汽膨胀或挥发时,潮气很可能会利用该处附着力不好的弱点,进而形成起泡。
4、溶剂挥发、涂膜固化起泡:转化型和非转化型涂料为固化完全,随着涂层固化和温度升高而释放挥发。
5、化学反应起泡:防腐设计不合理,底漆与胶层之间产生化学反应的化学物质导致起泡。不合适的底漆和胶带胶层,防腐系统可能因为没有必需的附着力或物理性能为高性能涂料提供合适的附着,导致某些溶剂从底材上脱离起鼓。另外,特殊的表面处理,如镀锌表面也肯能与做钝化处理时残留在上面的强酸碱起反应,形成气泡现象。
6、涮底漆过厚,部分溶剂没有完全挥发。残留溶剂处在溶剂挥发后最终变为空隙,形成起泡。
三、 怎样控制起泡现象
1、底漆生产过程控制:比如溶剂挥发率或树脂含水率、颜填料吸湿性等,调整配方。加强生产管理,避免使用可溶性的调料,使用溶剂要兼顾其挥发平衡,避免溶剂过多残留,在高湿环境中,使用渗透性低的基料。
2、防腐层设计合理规范:对不同的胶带选择同公司配套的底漆,防腐层与底漆的搭配选择。不同管径选择合适宽度的防腐胶带,易于施工,缠绕时受力均匀。
3、防腐施工的规范性:严格按照防腐施工工艺进行施工。施工时要避免高温、潮湿等不良气候环境,相对湿度不能高于85%,施工前如遇雨或凝露结霜等,要使其干燥后方可涂刷底漆进行防腐。注意表面粗糙度和表面清洁度,不得留下电解质、粉尘、油脂等影响涂料附着力的杂质,制品使用和保存时,尽量避免高温高湿环境,减少直接与水接触的机会。
四、防腐胶粘带缠绕出现气泡的成因
1、钢管表面处理质量直接影响了防腐质量.特别是对于螺纹钢管的螺旋焊缝处没有采取有效的处理措施,导致聚乙烯胶带缠绕后在焊缝处存在空隙,造成起泡。
2、管体与胶粘带的温度差。
3、涂刷底漆:在施工过程中,经过对管线表面预处理现场检查发现.施工单位往往在涂刷完底漆后.未等待底漆表干,就进行聚乙烯胶粘带缠绕,在天气较热或阳光充足情况下.缠绕胶带时,由于底漆中部分溶剂未挥发完,缠绕完毕后.地面放置时间较长.在造成气泡产生。
4、底漆刷好后未缠绕胶粘带,夜晚水汽凝露吸入,第二天再缠绕,即通俗说的底漆过夜。
5、缠绕不规范,手工缠绕时需用力均匀,保证胶粘带处于绷紧状态。聚乙烯防腐胶带没有真正意义上的缠到管体上,比如有间隙,与底漆为真正结合。
6、除锈不完全或者风沙较大的天气,管道表面有异物。
7、由于钢管吸热,而且防腐胶带的黑色更吸热,所以管体防腐后禁止暴晒,应根据要求储存。如正常气温在20℃,钢管的温度肯定在30℃以上,这是有悖于标准及施工要求的。而由于胶粘带的密封性比较好,导致水汽相当长的一段时间内透不出防腐层,导致气泡产生。只要施工时注意,这种问题是可以避免的。